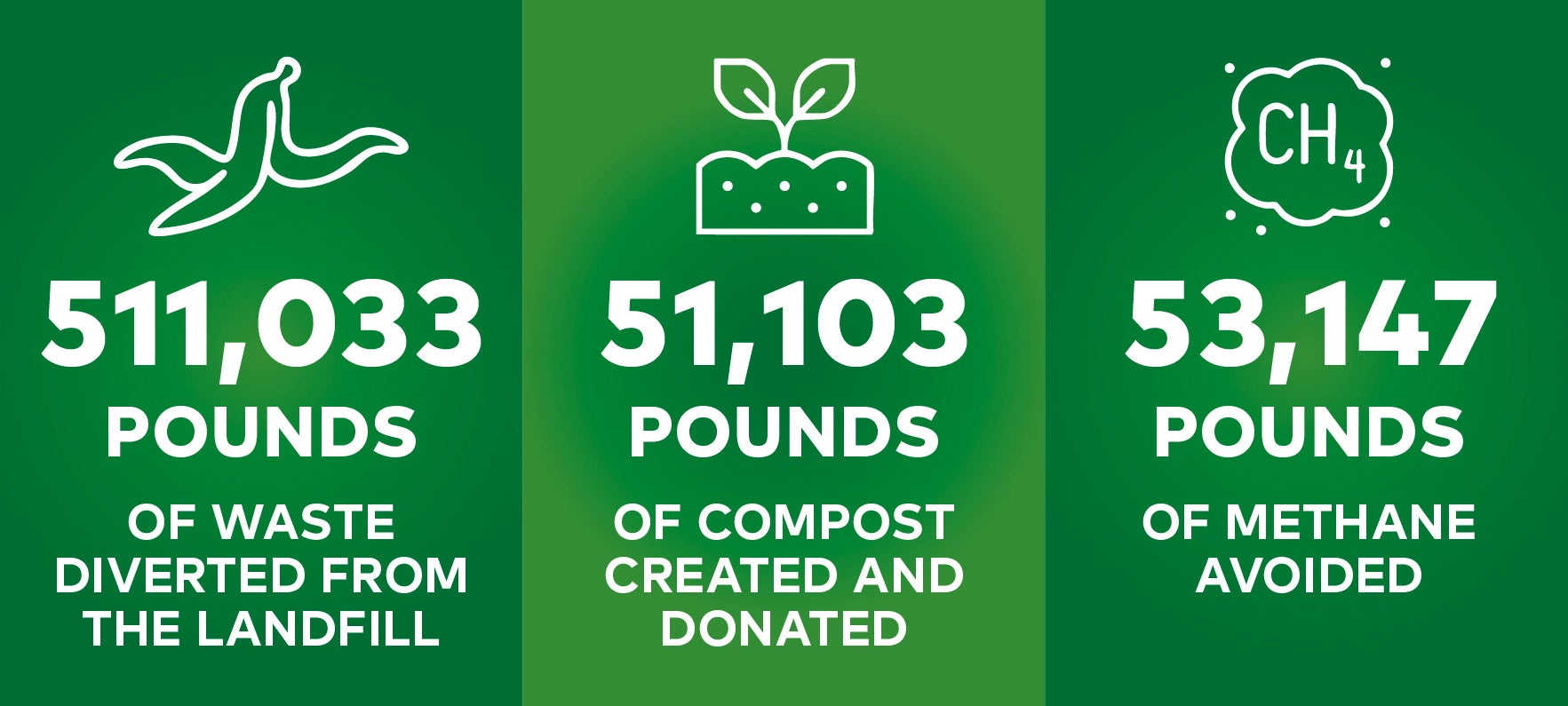
As a LEED Silver-certified building, the Raleigh Convention Center is dedicated to promoting sustainable practices within the facility and in the community. Since opening our doors in 2009, staying green has always been a priority. From the 350 tons of recycled steel that support our facility to the hundreds of thousands of pounds of waste we have diverted from landfills, we take steps both small and large to protect the planet. We're proud to be NC Green Travel-certified and the winner of the 2021 City of Raleigh Climate Action Awards for Energy and Water.
Our Environmental Policy
The Raleigh Convention Center is proud to be a space where communities flourish. As a facility where ideas, networks, and individuals grow, we also pride ourselves on being intentional, sustainable, and thoughtful stewards of our environment so that our local and global communities will thrive. We are committed to weighing the environmental impact of our business decisions, deploying initiatives that seek to conserve our planet’s natural resources, and seeking environmentally friendly solutions whenever possible. We strive to continuously reflect on and reassess our practices and policies through a sustainable lens. Raleigh Convention Center is committed to observing all Federal, state and local laws and ordinances aimed at protecting the environment.
Energy: Powering Your People
With 2,000 solar panels on the roof, our 500kW solar array is the second-largest convention center solar array in the U.S. They produce the amount of energy equal to the approximate annual energy use of 100 homes in North Carolina.
High bay motion-sensor LEDs in the 45k square foot underground delivery area reduce energy use by~18,480W/day.
We switched the lightbulbs in the 150k square foot exhibit hall to LED lights in 2015. Before the switch, we changed ~170 lightbulbs/year. This reduced energy use and maintenance by 318,230W/day.
Our efficient HVAC system reduces energy by 20% and is connected to our booking system which controls temperature for occupied/ unoccupied areas, providing a savings of nearly $15,000/year.
Water: Every Drop Counts
The facility cooling tower is supplemented by a natural flowing river under the venue, reducing water usage by 25,000 gallons/day.
On-demand water heaters have a 98% efficiency rating.
Low-flow toilets and timed faucets provide a 39% reduction in water.
We offer free water bottle fillers throughout the center, which minimizes demand for bottled water, which we are phasing out for a canned or boxed alternative.
Pollinator Friendly: We Keep Raleigh Buzzing and Growing
The gardens at the Raleigh Convention Center and Martin Marietta Center for the Performing Arts are planted and maintained by the City of Raleigh Parks and Recreation Department. Staff from both venues also volunteered in the planting of the new garden on Lichtin Plaza at the Martin Marietta Center for the Performing Arts, which was installed on September 18, 2019.
The Raleigh Convention Center's gardens are irrigation- and fertilizer-free. Their design was meant to mimic a dry river bed and features rocks taken from a variety of City of Raleigh parks.
Thanks to the success and health of the garden, a number of plants grown in the Raleigh Convention Center's planters have been moved to the city’s greenhouse to propagate new plants for other City parks.
Both gardens feature perennials that bloom at various times of the year. The Lichtin Plaza garden incorporates nearly 175 different types of grasses, nearly all native to North Carolina. These include 70 muhly grasses (Muhlenbergia ‘White Cloud’), 70 fountain grasses (Pennisetum ‘Karley Rose’) and 35 switch grasses (Panicum ‘Heavy Metal’). Some will grow to be 5' tall!
Throughout the year, the foliage in the Lichtin Plaza garden will showcase pinks, whites, and blues.
Catering: Reduce, Reuse, and Compost
We kicked off the first of its kind “Share a Meal” program, where clients can purchase extra meals to be matched by Sodexo Live! and then donated to the Central and Eastern Food Bank of North Carolina.
We are proud of our 40% average landfill diversion rate. Through composting with Raleigh-based CompostNow, we have diverted hundreds of thousands of pounds of food from the landfill since Fall of 2017.
The compost is then donated to Camden Street Learning Garden, which is operated by the Inter-faith Food Shuttle, a local nonprofit dedicated to ending hunger.
China is our default service but when clients request single-service items, we provide 100% biodegradable products that biodegrade in under 180 days.
Used cooking oil is converted to biofuel.
Eggs in all forms are sourced from cage-free producers and milk is hormone-free.
We are committed to using at least 10% of NC local, seasonal food products.
We utilize Ecolab products, a top-ranking company on the Global 500 Green Rankings List for biodegradable and environmentally safe products.
Our catering menu contains over 200 vegetarian items, 50+ vegan items, and 100+ gluten-free items. Our concession stands also feature vegetarian options, including the Beyond Burger.
Hydroponic gardens on site to test feasibility of large-scale hydroponics in-house.
Small Changes, Big Impact
We're proud to participate in a number of additional green initiatives, including the following:
Along with the City of Raleigh, the RCC has joined an international Lights Out effort by implementing a citywide initiative to protect migratory birds by turning off non-essential lighting in City facilities each night to prevent the potential for migratory bird collisions with buildings.
Conveniently located to six bus lines and within walking distance of the GoRaleigh Station
Mixed recycling bins located throughout the facility
Use of Green Seal-certified chemicals for 95% of cleaning products
100% organic pest management system
Use of Low-VOC carpeting, adhesives, and paint sealants
Implementation of an Air Quality Management Plan
EV charging station in parking deck
Outdoor Big Belly solar-powered trash compactor
Use of electric golf carts
Built Sustainably
The location was formerly a car dealership and, during construction, was discovered to be the site of a coal gasification plant from the late 1800s/early 1900s, making it a brownfield site.
100% of the 350 tons steel used in the construction of our building is recycled.
Defunct cell phone towers were repurposed as support beams for our facility.
Over 75% of the 9,512 tons of construction and demolition debris was diverted from landfills and incinerators.
The tan brick used in building is mined and manufactured from Charlotte, minimizing transportation costs.